In recent years, new warehouse automation technologies are gaining momentum because of the need to optimize labor time and reduce operating and order fulfillment costs. These needs have surfaced because of the rise of e-commerce (click here to read the effects of e-commerce in the warehouse industry)and higher customer demands, such as lower costs and faster response times, as stated by MHI.
In this article, we will explore why automation is an important solution to the challenges mentioned above. We’ll also discuss specific warehouse automation technologies that can effectively help you overcome these challenges.
Why Warehouse Automation is an Effective Solution to Current Challenges
As discussed in the intro, e-commerce, its effects on order fulfillment, and higher customer demands drive momentum toward the development and adoption of automation technologies. Automation solutions can improve warehouse operational efficiency and facilitate quicker and more accurate order fulfillment, which, in turn, leads to an enhanced customer experience.
4 Effective Warehouse Automation Solutions
Automated Storage and Retrieval Systems (AS/RS)
Automated Storage and Retrieval Systems (AS/RS) refer to a variation of computer-controlled systems for automatically storing and retrieving goods from defined storage locations in a warehouse with precision, accuracy, and speed, as described by MHI. These systems automate warehouse processes such as order picking, storage, kitting, consolidation, assembly, replenishment, etc.
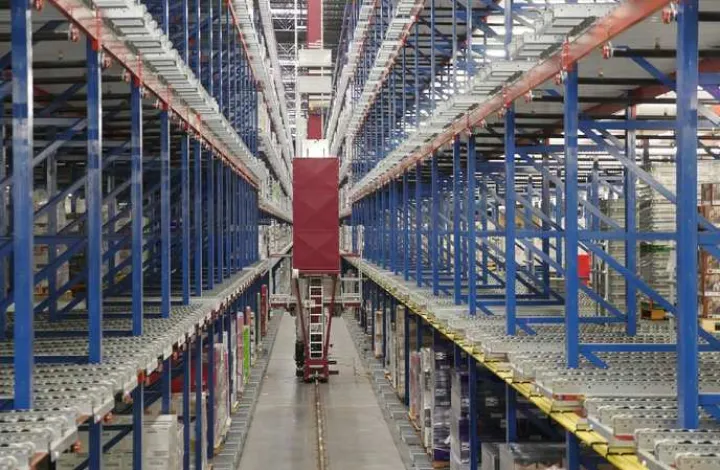
Source: Westfalia
Some benefits of using an AS/RS system include floor space optimization, improved accuracy, and increased productivity. Its main disadvantage is the significant investment required to install, maintain, and operate it. Consequently, AS/RS systems are preferable in warehouses that handle a large number of products.
Pick-to-Light Systems
The Pick-to-Light System is a low-automation technology that supports the pickers in the warehouse with light signals. It uses a light device mounted on racks, shelves, and workstations to guide employees to the correct product locations and quantities required to fulfill the order. When all lights turn off, the picker has finished the current order and can move on to the next one.
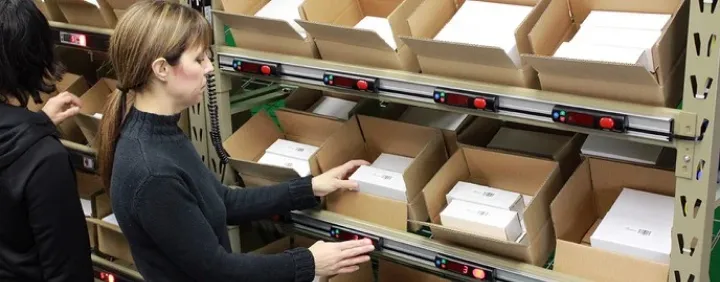
Source: Lightning Pick
Pick-to-light systems have been acknowledged as the fastest operator-based picking strategy available to execute broken case quantity order fulfillment operations. They provide an accurate and efficient method of paperless picking, sorting, and assembling of products. In dense picking environments, the high installation cost is counterbalanced by many picks per unit of distance. However, they are not ideal for warehouses that require frequent layout rearrangements, and it can be challenging to support simultaneous picking by several pickers.
Autonomous Mobile Robots (AMRs)
Autonomous Mobile Robots (AMRs) can sense physical surroundings and move through the warehouse without supervision. While traditional AGVs require external guidance, AMRs can operate without being directly supervised by a human operator and perform several activities, from transporting materials and goods to facilitating an existing pick strategy. They usually perform better in warehouses with high-volume and high-labor requirements since this helps reduce travel time. However, with warehouses that handle extremely weighty materials, these robots are not equipped to handle them yet.
According to the Guide to Autonomous Mobile Reports of CONVEYCO, typically, AMRs can be split into three functionalities:
- Move inventory within a facility
- Assist in automating the warehouse picking process
- Flexible sortation solution
Autonomous Mobile Robots provide value to warehouse operations in the following senses:
- Flexibility and scalability: Initial deployment can start with a few units with the flexibility and scalability to add and reduce as necessary.
- Reduced labor costs: The less time workers spend traveling, the more time they spend fulfilling orders.
- Increase warehouse safety: Support the workers by taking over heavy lifting and minimizing the involvement of humans.
Unmanned Aerial Vehicles (UAVs)
Much like autonomous robots, lightweight Unmanned Aerial Vehicles (UAVs) are being incrementally adopted for warehouse inventory management. Recent advancements have been made in UAV technology, including sensors and visual-based navigation. These advancements are now helping with tasks like inventory audits, item searches, and stocktaking.
Unmanned Aerial Vehicles (UAVs) offer several benefits, including increased efficiency, enhanced accuracy, and greater safety. However, there are also disadvantages, such as a high initial investment and technological limitations, such as battery life. Also, UAVs are preferable in relatively large warehouses with long corridors and high shelves.
Summary
Each of the warehouse automation solutions discussed above has its advantages and disadvantages, as summarized in the table below:
The four warehouse automation solutions have seen an increase in adoption since they can help companies sustain and thrive amongst the challenges posed by e-commerce, such as faster fulfillment times and lower costs. By investing in these technologies, you can achieve greater efficiency and accuracy, which can help increase your perfect order rate and provide better service to your customers.
If you want to learn more about Warehouse Digitalization and optimizing warehouse processes, you can follow us on LinkedIn, YouTube, X, or Facebook. If you have other inquiries or suggestions, please contact us here. We’ll be happy to hear from you.